Paper, a versatile material that we encounter every day, holds within it a fascinating blend of artistry and scientific ingenuity. From the fine pages of a novel to the delicate tissue used for hygiene, paper manufacturing is a process that intertwines craftsmanship with technological advancements. In this article, we will delve into the depths of this process, providing a comprehensive guide to the art and science behind the creation of paper. Whether you are curious about the intricate details of paper manufacturing or seeking to gain insight into the specific production of toilet paper, this exploration will enlighten you. So, let us embark on this journey to unveil the secrets behind the evolution of paper, from its humble origins to the refined techniques employed today. Prepare to unravel the extraordinary story of the creation of paper and the wonders that lie within its fibers.
1. The Pulping Process
In the fascinating world of paper manufacturing, the pulping process stands as a crucial first step. This process extracts the fibers from wood, transforming it into the raw material needed for paper production. There are two primary methods used in this process: mechanical pulping and chemical pulping.
Mechanical pulping involves grinding the wood into small pieces, which are then treated with steam and chemicals to soften the fibers. The resulting mixture is passed through a series of screens to remove impurities and separate the fibers. This method is often used for producing newsprint and other lower quality papers.
Paper Manufacturers
On the other hand, chemical pulping, as the name suggests, utilizes chemicals to separate the fibers. The most common form of chemical pulping is the Kraft process, where wood chips are cooked in a solution of chemicals, such as sodium hydroxide and sodium sulfide. This breaks down the lignin, a natural adhesive that holds the fibers together, allowing them to be separated more easily. The resulting pulp is then washed and bleached to achieve the desired quality.
Both mechanical and chemical pulping have their merits and are used in different scenarios based on the desired properties of the paper. Understanding these processes is essential in the world of paper manufacturing, whether you are producing a fine writing paper or a humble roll of toilet paper.
Please let me know if there is anything else I can assist you with.
2. Papermaking: From Pulp to Paper
In the fascinating process of papermaking, pulp is transformed into the versatile material we know as paper. This intricate procedure involves several stages that ensure the creation of high-quality paper products. Let’s take a closer look at the journey from pulp to paper.
Firstly, the papermaking process starts with the preparation of the pulp. Pulp can be derived from various sources, including wood fibers or recycled paper. To obtain a suitable pulp consistency, the raw materials are mixed with water and broken down into small fibers. This mixture is then subjected to refining, which involves mechanical action to enhance the pulp quality further.
Next, the refined pulp undergoes the process of sheet formation. In this step, the pulp is dispersed uniformly in a large vat of water. A wire mesh screen is submerged into the vat, and as it is slowly lifted, it catches the pulp fibers, forming a thin layer. Excess water drains away, leaving a mat of intertwined fibers on the screen.
Once the initial sheet has formed, it enters the pressing section. This is where excess water is squeezed out, making the sheet more compact. Pressing involves passing the wet sheet between two large rolls that exert pressure, removing water and consolidating the fibers. This step brings the sheet closer to its final thickness and also improves its strength.
The transformed mat of wet paper then makes its way to the drying section. Here, various methods are employed to remove the remaining moisture and completely dry the paper. Depending on the scale of production, drying can occur through air-drying or with the use of heated drying cylinders. The paper travels through a series of heated rollers, where the heat and pressure help evaporate the remaining water, leaving a perfectly dried sheet.
As we conclude this section, remember that the papermaking process is not limited to a single type of paper. Whether it’s producing everyday writing paper or a specialized product like toilet paper, these steps serve as the foundation for various paper manufacturing processes, each tailored and optimized for its intended use. Understanding the intricacies of papermaking helps us appreciate the efforts behind the creation of this ubiquitous material.
3. The Production of Toilet Paper
Toilet paper manufacturing is a fascinating process that involves several key steps. Here, we will explore the art and science behind the creation of this essential product.
Pulp Creation:
Toilet paper begins its journey as wood pulp. Logs are carefully selected and debarked before being cut into smaller pieces. These wood pieces are then chipped and subjected to a chemical process that breaks down the lignin, separating the pulp fibers. The resulting pulp is then cleaned and refined, removing any impurities and producing a smooth, workable material.Paper Formation:
Once the pulp is ready, it is time for the paper formation stage. The pulp is mixed with water to create a slurry, which is then sprayed onto a continuous wire mesh. As the water drains away, the fibers start to bond together, forming a thin paper sheet. This sheet then goes through a pressing process to remove even more water and improve the paper’s density.Finishing Touches:
Toilet paper is known for its softness and absorbency, and achieving these qualities requires additional steps. The paper sheet passes through a series of heated drying cylinders, which evaporate any remaining moisture. It then undergoes a process called creping, where the paper is scraped off the drying cylinders with a metal blade. This gives the toilet paper its distinctive texture and increases its softness.
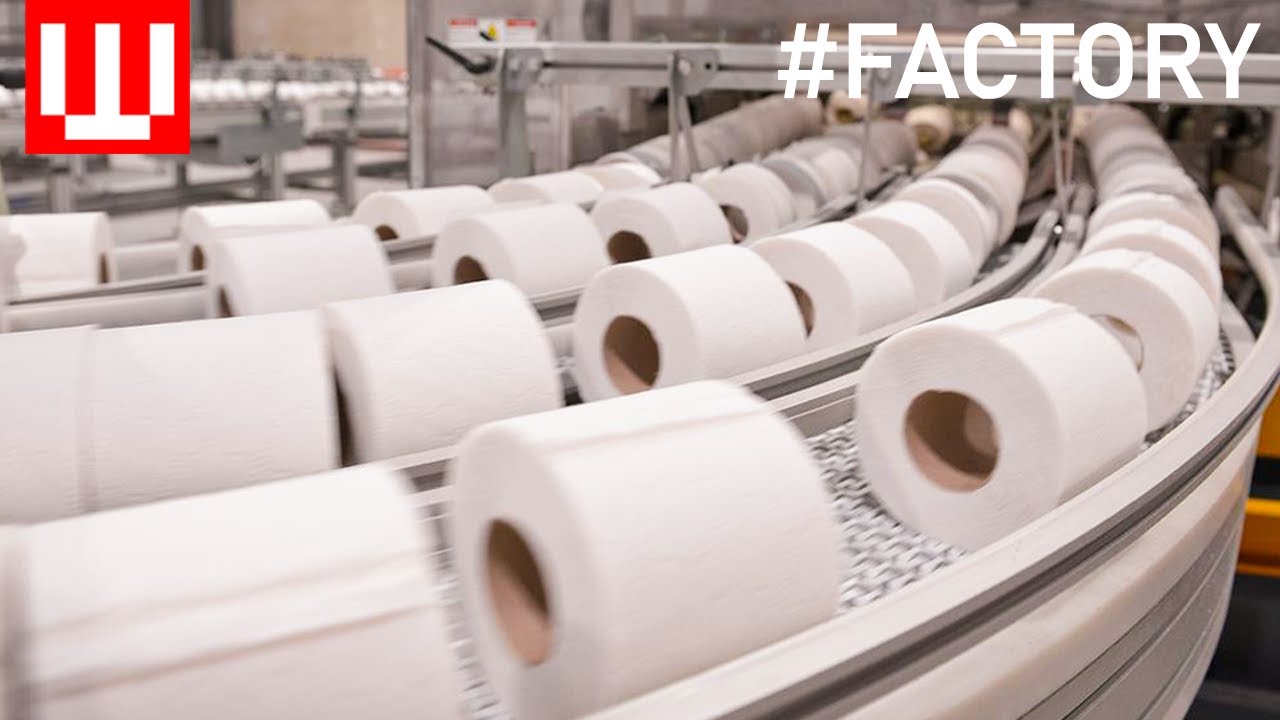
After creping, the paper is wound onto large rolls, which are then sent to be cut into individual toilet paper rolls. These rolls are packaged and prepared for distribution, ready to be used by countless people around the world.